2. Configuration
2.1 Connect to the CVS
The CVS has built-in wireless (WiFi) and wired Ethernet network connectivity. The wireless radio can be configured to use either 2.4 GHz or 5 GHz bands and supports hotspot or client modes. It can also be disabled. Wired Ethernet provides optional Gigabit LAN connectivity. Initial connection can be either wireless or wired and networking settings can be modified from the CVS user interface.
2.1.1 Wireless Connection
By default, the CVS is configured as a wireless hotspot with the following settings:
Connect to the hotspot with any device with built-in 2.4 GHz WiFi and a web-browser. Once wireless connection is established, the CVS user interface can be opened in a web browser at the URL specified.
Wireless networking configuration can be modified in the WiFi section of System configuration, accessible from the CVS user interface menu. Please connect via wired Ethernet to modify wireless configuration. Do not connect wired and wireless interfaces on the same network subnet.
2.1.2 Wired Ethernet Connection
By default, the CVS wired Ethernet (LAN) port is configured with a static IP address as follows:
Connect via Ethernet cable from any device with a built-in Ethernet port and a web browser. Set the IP address of your device to a different static IP address on the 192.168.0.0 subnet. Once network connection has been established, the CVS user interface can be opened in a web browser at the URL specified.
Wired Ethernet configuration can be modified in the Ethernet section of System configuration, accessible from the CVS user interface menu. Note that if a static or automatic (DHCP) Router (Gateway) is set then then wired Ethernet will be used for all Wide Area Network (WAN) connections, otherwise wireless will be used. Do not connect wired and wireless interfaces on the same network subnet.
2.1.3 Log in to the CVS user interface
When the CVS user interface is opened in a web browser for the first time, a login page will be displayed. Login with the following credentials:
Login: admin
Password: loadscan
After logging in as admin, login options and passwords can be changed in the Users section of System configuration, accessible from the CVS user interface menu.
2.2 System Configuration
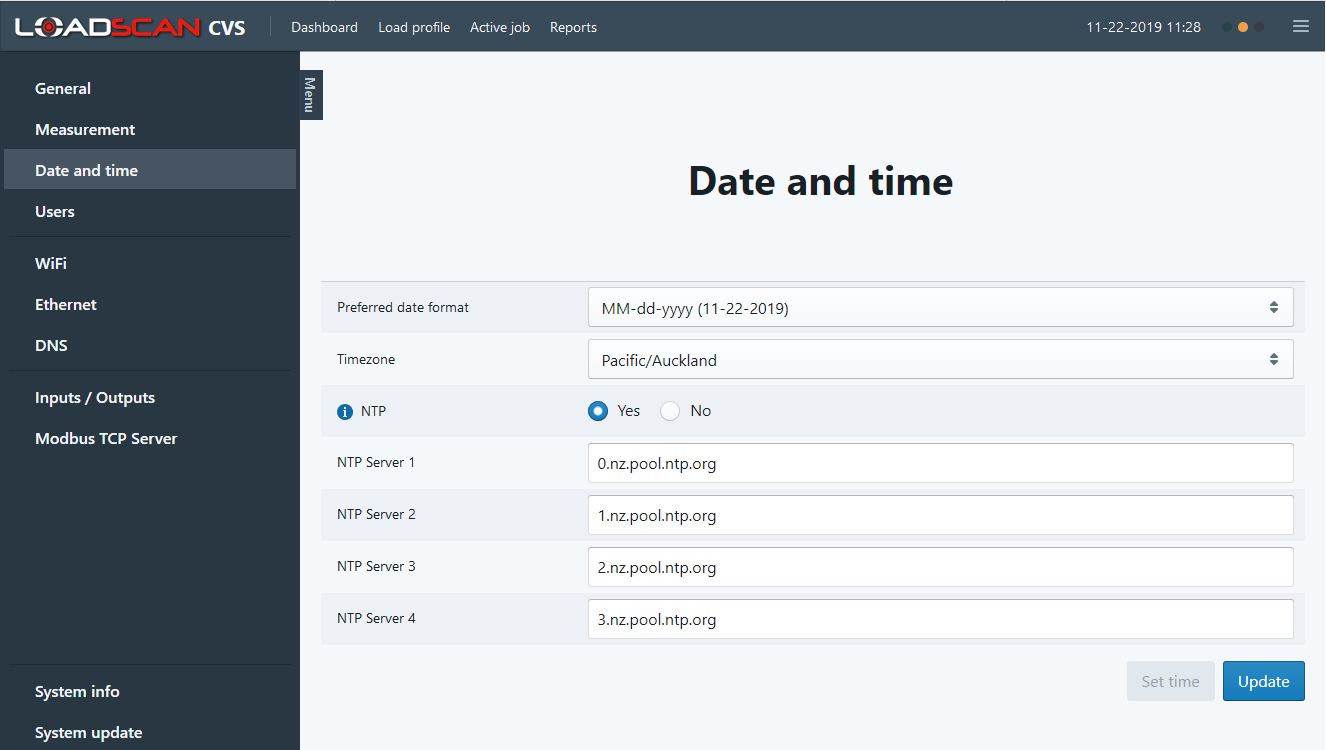
Please review all settings and modify to suit your region, application and networking environment. Additional information is available for some configuration parameters by tapping/hovering on the icon.
2.3 Measurement Configuration
2.3.1 Units
2.3.2 Sensitivity
Sensitivity controls how responsive the measurement is to very low levels of material on the belt. When this is set to High (default) measurement is triggered by the lowest detectable level of material on the belt. If vibration and movement of the belt result in measurement when the belt is empty, then try changing sensitivity to Medium or Low. This will reduce unwanted measurement but may also result in no measurement when the belt is very lightly loaded. The best setting should be experimentally determined.
2.3.3 Belt speed
Configure the belt speed input method and calibration as required.
If an inductive speed sensor is fitted:
Note that the current belt speed is displayed to maximum possible resolution on the Belt profile page, accessible from the user interface menu. This allows for accurate comparison of calibrated belt speed.
If an inductive speed sensor has not been fitted and the belt speed is a known constant value:
Note that the fixed speed value can be updated via the HTTP RESTful API.
Optionally, set Use belt running control signal to Yes to control when the belt is running with an external control signal. In this case belt speed will be forced to zero when the signal is not set. This is intended for use with a fixed speed setting but will work for any speed source. A digital switching input or Modbus coil must be mapped to the ‘Belt running’ control signal input (see 2.4.1 Assign control signals to inputs).
If the belt speed is being measured by an external system and sent to the CVS by a Modbus TCP client or 4-20 mA current loop input (add-on CVS-I/O box required):
In this case a Modbus holding register or CVS-I/O analogue input channel must be mapped to the ‘Belt speed’ control value input (see 2.4 Input/Output Configuration).
To enable belt speed averaging, set the number of seconds over which to average in Speed averaging period. Maximum averaging period is 600 seconds (10 minutes). Set zero to disable averaging. Note that averaging over a long period of time can result in delayed response to sudden changes such as belt start/stop or load material start/stop.
2.3.4 Flow rate
To enable averaging for volume and mass flow rate, set the number of seconds over which to average in Flow rate averaging period. Maximum averaging period is 600 seconds (10 minutes). Set zero to disable averaging. Note that averaging over a long period of time can result in delayed response to sudden changes such as belt start/stop or load material start/stop.
2.3.5 Load height
Load height is a measure of the height/depth of the load material above the belt. Set Load height method to one of the following:
Centre height is the vertical load height at the centre of the belt.
Maximum height is the maximum vertical load height. This is the deepest point on the load and may not necessarily occur at the highest point on the top surface of the load.
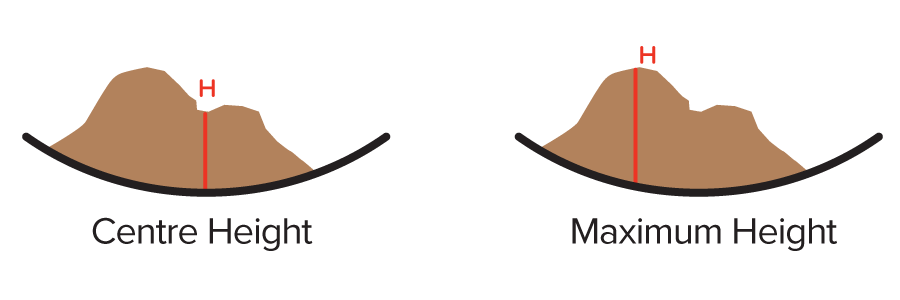
To enable load height averaging, set the number of seconds over which to average in Load height averaging period. Maximum averaging period is 600 seconds (10 minutes). Set zero to disable averaging. Note that averaging over a long period of time can result in delayed response to sudden changes such as belt start/stop or load material start/stop.
2.3.6 Load position
Load Position is a measure of the distribution of the load material across the belt and reports the position of the centre-of-mass of the load material, computed from the transverse cross-section of the load on the belt. Load position is reported in the range 0 – 1, where a value of 0 corresponds to the left-hand end of the defined zero profile and a value of 1 corresponds in the right-hand end. A value of 0.5 corresponds to the centre of the defined zero profile. If the zero profile end points are symmetric about the laser centreline, then a value of 0.5 also corresponds to the point directly below the laser.
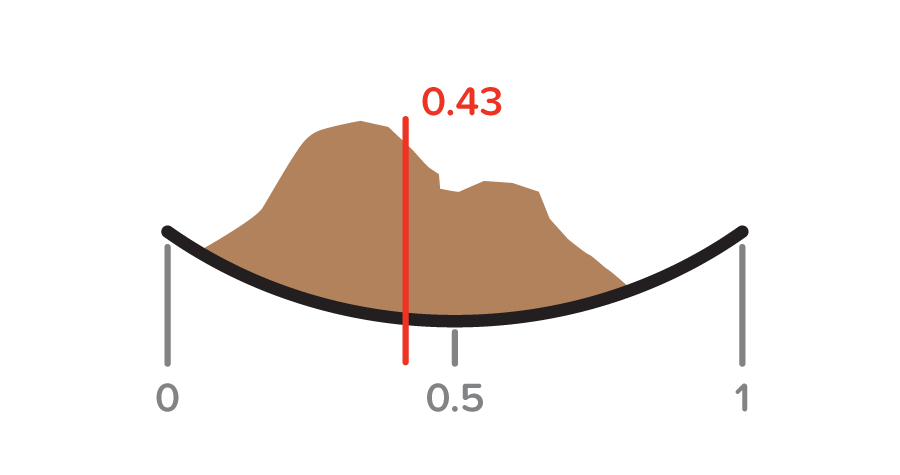
Load position will not be computed if the load height is less than Minimum load height. In this case a value of 0.5 (belt centre) is reported.
To enable load position averaging, set the number of seconds over which to average in Load position averaging period. Maximum averaging period is 600 seconds (10 minutes). Set zero to disable averaging. Note that averaging over a long period of time can result in delayed response to sudden changes such as belt start/stop or load material start/stop.
2.4 Input/Output Configuration
The CVS provides inputs and outputs for external monitoring and control via built-in Modbus TCP Server or optional add-on CVS-I/O box with 4-20 mA current loop analogue inputs and outputs and digital switching inputs and outputs. Live measurement values, status signals, control values and control signals can be mapped to Modbus registers or I/O channels.
If the CVS-I/O box is installed, then the I/O Hardware setting in the General section of System configuration must be set to CVS External I/O. General input and output settings are available in the Inputs/Outputs section of System configuration. The image below shows an example configuration only.
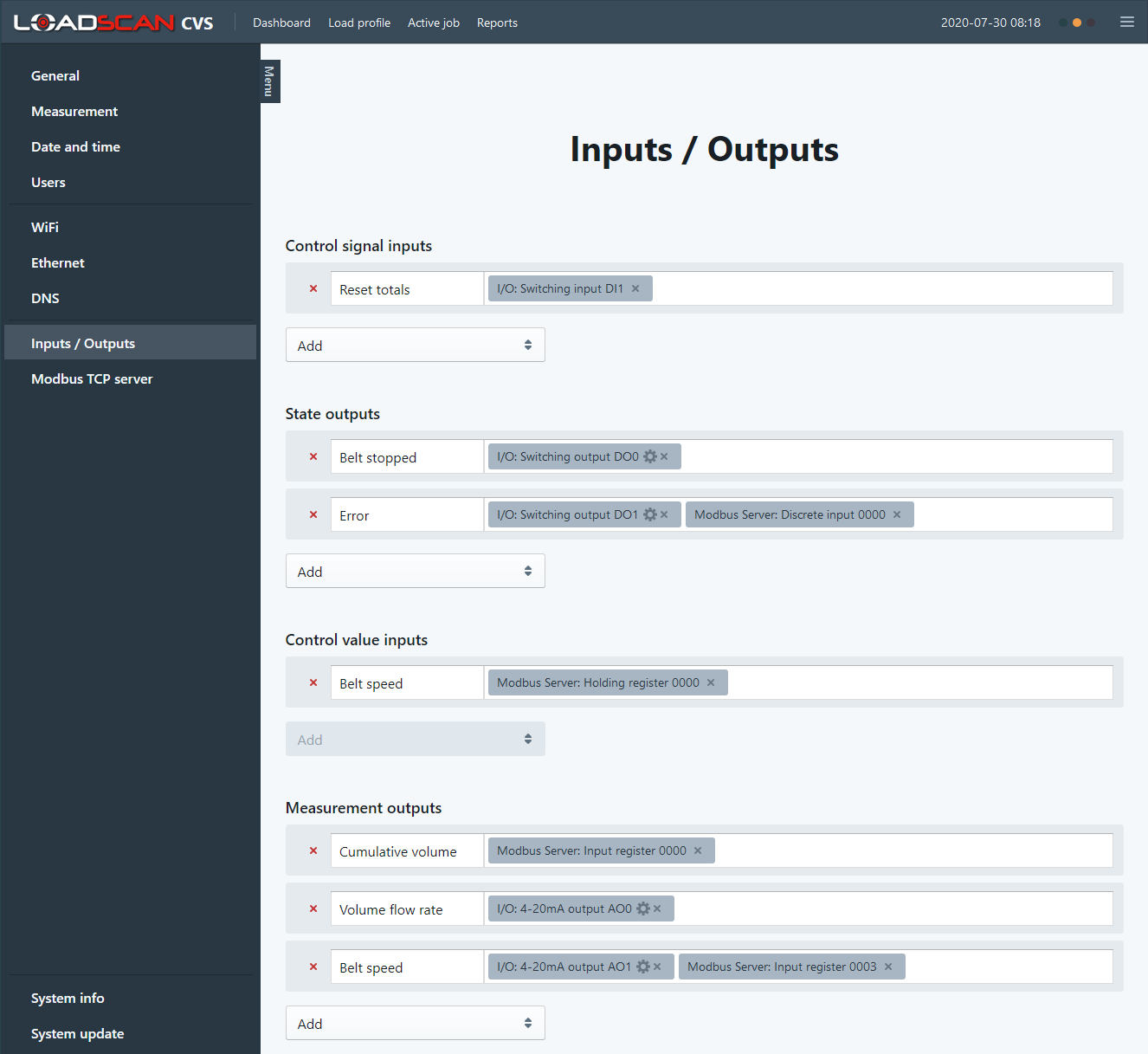
2.4.1 Control signal inputs
The following control signals can be supplied by external control systems. These can be read from Modbus coils or from digital switching inputs:
Belt running: If Use belt running control signal is set in the Belt speed section of Measurement configuration then belt speed will be forced to zero when this signal is not set. This is intended for use with a fixed speed setting but will work for any speed source.
Reset totals: a rising edge or 0 > 1 transition on this signal will reset cumulative volume/mass totals to zero. For idle state measurement this has the same effect as pushing the Reset button on the Dashboard. If a job is running this is the same as resetting the active job on the Active job page.
To assign a control signal to an input channel, click on the Add button in the Control signal inputs section of Inputs/Outputs and select the required control signal. This creates a new row for the selected signal. Click in the mapping area of this row to select an available input channel. A control signal can only be mapped to one input channel.
Modbus coils: coils must be defined before they can be selected as an input channel (see 2.5 Modbus TCP Server Configuration).
Digital switching inputs: If the control signal is not a pulse type input the Active high checkbox can be un-checked when adding the channel to invert the digital input logic. This setting can be edited at any time by clicking on the settings icon () on the assigned channel. See LoadScan CVS-I/O Installation Guide document for signal requirements and wiring.
2.4.2 Status signal outputs
The following status signals can be sent to external monitoring and control systems or directly control belt start/stop, activate status indicator lights and so on. These can be written to Modbus discrete inputs or drive digital switching outputs:
- Idle: measurement mode is operational, but no job is active (unassigned measurement only).
- Job active: a job is running. This signal can be used, for example, to start the belt automatically when a job is started and stop the belt when the job is stopped.
- Job target reached: target volume/weight for the active job has been reached and the job is still running. This signal can be used, for example, to control a visual indicator to advise the operator that the job is ready to be manually stopped.
- Black belt: belt is running (belt speed greater than zero) but there is no material on the belt.
- Belt stopped: belt speed is zero.
- Warning: non-fatal error condition requiring operator intervention is active.
- Error: a fatal error condition requiring operator intervention is active (measurement stopped).
To assign a status signal to an output channel, click on the Add button in the State outputs section of Inputs/Outputs and select the required status signal. This creates a new row for the selected signal. Click in the mapping area of this row to select an available output channel. One status signal can be assigned to multiple output channels. Multiple status signals can also be assigned to one output channel. In this case an output will be active when any of the assigned status signals are set.
Modbus discrete inputs: discrete inputs must be created before they can be selected as an output channel (see 2.5 Modbus TCP Server Configuration).
Digital switching outputs: The Active high checkbox can be un-checked when adding the channel to invert the digital output logic. This setting can be edited at any time by clicking on the settings icon () on the assigned channel. See LoadScan CVS-I/O Installation Guide document for signal requirements and wiring.
2.4.3 Control value inputs
The following control values can be supplied by external control systems. They can be read from Modbus holding registers or 4-20 mA current loop analogue inputs:
- Belt speed: If speed source is set to Belt speed input in the Belt speed section of Measurement configuration then this value sets the belt speed.
To assign a control value to an input channel, click on the Add button in the Control value inputs section of Inputs/Outputs and select the required control value. This creates a new row for the selected value. Click in the mapping area of this row to select an available input channel. A control value can only be assigned to one output.
Modbus holding registers: holding registers must be created before they can be selected as an input channel (see 2.5 Modbus TCP Server Configuration).
Analogue inputs: the control values corresponding to the 4 mA and 20 mA end-points must be specified at the time of adding the channel and can be edited at any time by clicking on the settings icon () on the assigned channel. See LoadScan CVS-I/O Installation Guide document for analogue input signal requirements and wiring.
2.4.4 Measurement value outputs
The following measurement values can be sent to external monitoring and control systems. They can be written to Modbus input registers or 4-20 mA current loop analogue outputs:
- Cumulative volume: the current total volume
- Cumulative mass: the current total weight
- Volume flow rate: the current volume flow rate
- Mass flow rate: the current mass flow rate
- Belt speed: the current belt speed
- Load height: the current load height
- Load position: the current load position
To assign a measurement value to an output channel, click on the Add button in the measurement outputs section of Inputs/Outputs and select the required measurement. This creates a new row for the selected measurement. Click in the mapping area of this row to select an available output channel. One measurement value can be output to multiple output channels, but a single output channel can only be assigned to one measurement.
Modbus input registers: input registers must be created before they can be selected as an output channel (see 2.5 Modbus TCP Server Configuration).
Analogue outputs: the control values corresponding to the 4 mA and 20 mA end-points must be specified at the time of adding the channel and can be edited at any time by clicking on the settings icon () on the assigned channel. See LoadScan CVS-I/O Installation Guide document for analogue input signal requirements and wiring.
2.5 Modbus TCP Server Configuration
Live measurement values, status signals, control values and control signals can be mapped to Modbus registers. Modbus TCP Server settings are available in the Modbus TCP Server section of System Configuration. This document assumes the reader is familiar with Modbus TCP. The image below shows an example configuration only.
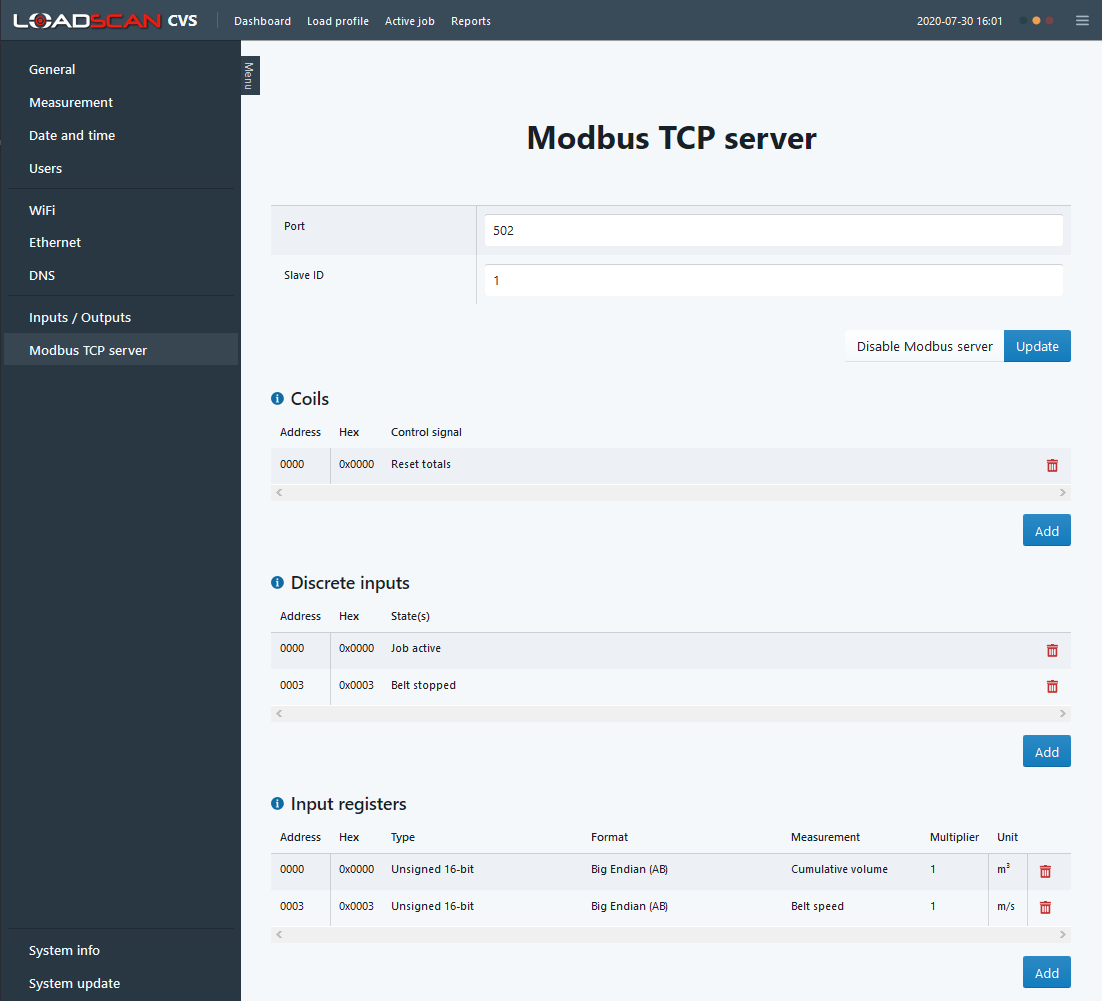
Modbus configuration is very flexible. The CVS does not have a fixed register table. Modbus registers can be added and removed as required. Register addresses can also be set as desired and multiple data formats are available.
The Modbus TCP server must be enabled with the Enable Modbus server button and can be disabled at any time without losing existing configuration.
Once Modbus registers have been defined, they can be used as input or output channels and assigned to different measurement or control values or signals (see 2.4 Input/Output Configuration).
The following Modbus register types can be added:
- Coils: these are discrete CVS inputs (outputs from remote Modbus TCP client) and can be assigned to control signal inputs.
- Discrete inputs: these are discrete CVS outputs (inputs to remote Modbus TCP client) and can be assigned to status signals.
- Holding registers: these are value inputs to the CVS (outputs from remote Modbus TCP client) and can be assigned to control values. Multiple data formats are available, and a divider can optionally be applied to the value read from a holding register.
- Input registers: these are CVS outputs (inputs to remote Modbus TCP client) and can be assigned to measurement values. Multiple data formats are available, and a multiplier can optionally be applied to the value before writing to an input register.
To add a Modbus register, click the Add button for the required type and enter the requested details in the pop-up dialog. After Modbus objects have been created, they automatically appear in the Input/Output section of System Configuration, with the selected signal or value assignment. A Modbus register can be re-assigned to a different signal or value or the assignment removed. Removing the assignment in Input/Output configuration clears the assignment but does not remove the Modbus register from Modbus TCP Server configuration. It can be removed from Modbus TCP Server configuration or re-assigned in Input/Output configuration.
In this Article
2. Configuration
2.1 Connect to the CVS
The CVS has built-in wireless (WiFi) and wired Ethernet network connectivity. The wireless radio can be configured to use either 2.4 GHz or 5 GHz bands and supports hotspot or client modes. It can also be disabled. Wired Ethernet provides optional Gigabit LAN connectivity. Initial connection can be either wireless or wired and networking settings can be modified from the CVS user interface.
2.1.1 Wireless Connection
By default, the CVS is configured as a wireless hotspot with the following settings:
Connect to the hotspot with any device with built-in 2.4 GHz WiFi and a web-browser. Once wireless connection is established, the CVS user interface can be opened in a web browser at the URL specified.
Wireless networking configuration can be modified in the WiFi section of System configuration, accessible from the CVS user interface menu. Please connect via wired Ethernet to modify wireless configuration. Do not connect wired and wireless interfaces on the same network subnet.
2.1.2 Wired Ethernet Connection
By default, the CVS wired Ethernet (LAN) port is configured with a static IP address as follows:
Connect via Ethernet cable from any device with a built-in Ethernet port and a web browser. Set the IP address of your device to a different static IP address on the 192.168.0.0 subnet. Once network connection has been established, the CVS user interface can be opened in a web browser at the URL specified.
Wired Ethernet configuration can be modified in the Ethernet section of System configuration, accessible from the CVS user interface menu. Note that if a static or automatic (DHCP) Router (Gateway) is set then then wired Ethernet will be used for all Wide Area Network (WAN) connections, otherwise wireless will be used. Do not connect wired and wireless interfaces on the same network subnet.
2.1.3 Log in to the CVS user interface
When the CVS user interface is opened in a web browser for the first time, a login page will be displayed. Login with the following credentials:
Login: admin
Password: loadscan
After logging in as admin, login options and passwords can be changed in the Users section of System configuration, accessible from the CVS user interface menu.
2.2 System Configuration
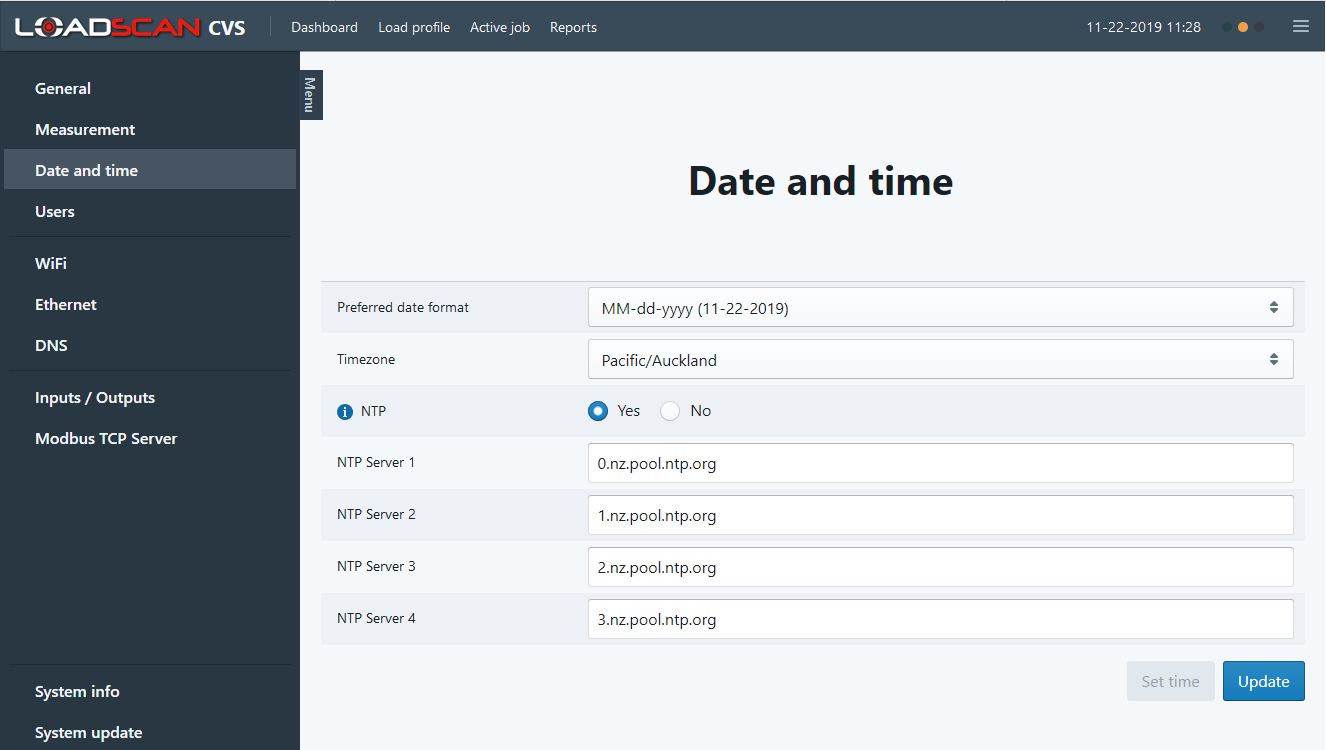
Please review all settings and modify to suit your region, application and networking environment. Additional information is available for some configuration parameters by tapping/hovering on the icon.
2.3 Measurement Configuration
2.3.1 Units
2.3.2 Sensitivity
Sensitivity controls how responsive the measurement is to very low levels of material on the belt. When this is set to High (default) measurement is triggered by the lowest detectable level of material on the belt. If vibration and movement of the belt result in measurement when the belt is empty, then try changing sensitivity to Medium or Low. This will reduce unwanted measurement but may also result in no measurement when the belt is very lightly loaded. The best setting should be experimentally determined.
2.3.3 Belt speed
Configure the belt speed input method and calibration as required.
If an inductive speed sensor is fitted:
Note that the current belt speed is displayed to maximum possible resolution on the Belt profile page, accessible from the user interface menu. This allows for accurate comparison of calibrated belt speed.
If an inductive speed sensor has not been fitted and the belt speed is a known constant value:
Note that the fixed speed value can be updated via the HTTP RESTful API.
Optionally, set Use belt running control signal to Yes to control when the belt is running with an external control signal. In this case belt speed will be forced to zero when the signal is not set. This is intended for use with a fixed speed setting but will work for any speed source. A digital switching input or Modbus coil must be mapped to the ‘Belt running’ control signal input (see 2.4.1 Assign control signals to inputs).
If the belt speed is being measured by an external system and sent to the CVS by a Modbus TCP client or 4-20 mA current loop input (add-on CVS-I/O box required):
In this case a Modbus holding register or CVS-I/O analogue input channel must be mapped to the ‘Belt speed’ control value input (see 2.4 Input/Output Configuration).
To enable belt speed averaging, set the number of seconds over which to average in Speed averaging period. Maximum averaging period is 600 seconds (10 minutes). Set zero to disable averaging. Note that averaging over a long period of time can result in delayed response to sudden changes such as belt start/stop or load material start/stop.
2.3.4 Flow rate
To enable averaging for volume and mass flow rate, set the number of seconds over which to average in Flow rate averaging period. Maximum averaging period is 600 seconds (10 minutes). Set zero to disable averaging. Note that averaging over a long period of time can result in delayed response to sudden changes such as belt start/stop or load material start/stop.
2.3.5 Load height
Load height is a measure of the height/depth of the load material above the belt. Set Load height method to one of the following:
Centre height is the vertical load height at the centre of the belt.
Maximum height is the maximum vertical load height. This is the deepest point on the load and may not necessarily occur at the highest point on the top surface of the load.
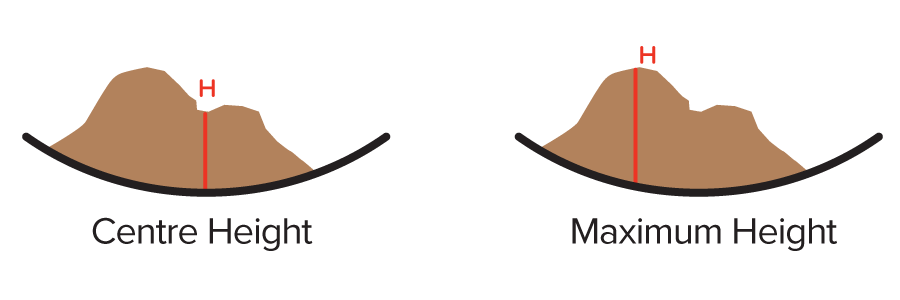
To enable load height averaging, set the number of seconds over which to average in Load height averaging period. Maximum averaging period is 600 seconds (10 minutes). Set zero to disable averaging. Note that averaging over a long period of time can result in delayed response to sudden changes such as belt start/stop or load material start/stop.
2.3.6 Load position
Load Position is a measure of the distribution of the load material across the belt and reports the position of the centre-of-mass of the load material, computed from the transverse cross-section of the load on the belt. Load position is reported in the range 0 – 1, where a value of 0 corresponds to the left-hand end of the defined zero profile and a value of 1 corresponds in the right-hand end. A value of 0.5 corresponds to the centre of the defined zero profile. If the zero profile end points are symmetric about the laser centreline, then a value of 0.5 also corresponds to the point directly below the laser.
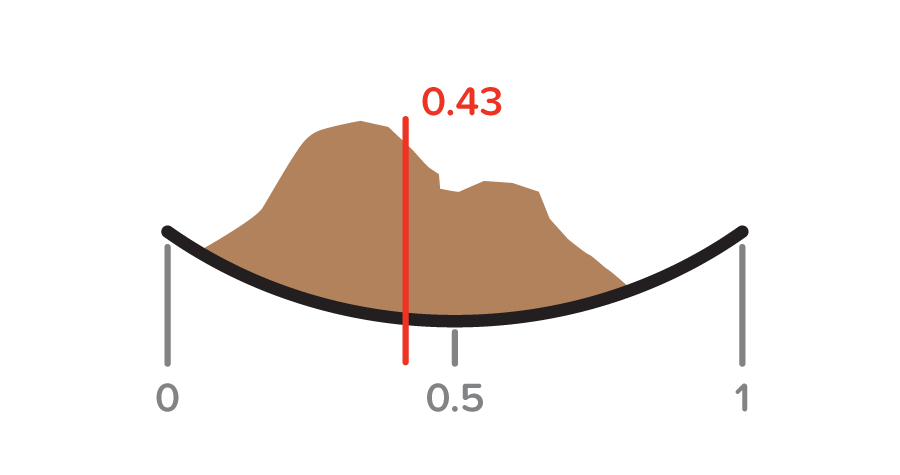
Load position will not be computed if the load height is less than Minimum load height. In this case a value of 0.5 (belt centre) is reported.
To enable load position averaging, set the number of seconds over which to average in Load position averaging period. Maximum averaging period is 600 seconds (10 minutes). Set zero to disable averaging. Note that averaging over a long period of time can result in delayed response to sudden changes such as belt start/stop or load material start/stop.
2.4 Input/Output Configuration
The CVS provides inputs and outputs for external monitoring and control via built-in Modbus TCP Server or optional add-on CVS-I/O box with 4-20 mA current loop analogue inputs and outputs and digital switching inputs and outputs. Live measurement values, status signals, control values and control signals can be mapped to Modbus registers or I/O channels.
If the CVS-I/O box is installed, then the I/O Hardware setting in the General section of System configuration must be set to CVS External I/O. General input and output settings are available in the Inputs/Outputs section of System configuration. The image below shows an example configuration only.
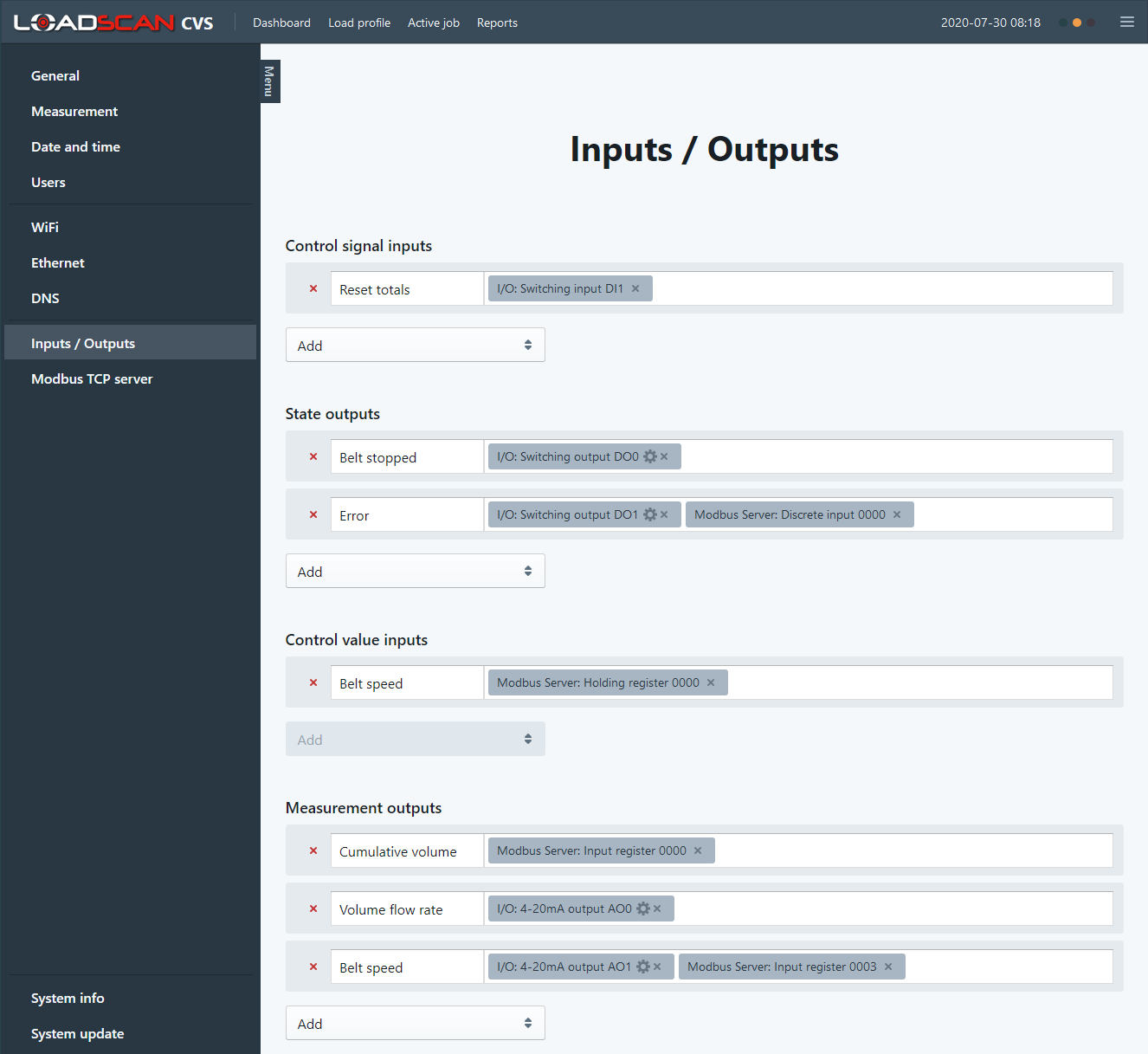
2.4.1 Control signal inputs
The following control signals can be supplied by external control systems. These can be read from Modbus coils or from digital switching inputs:
Belt running: If Use belt running control signal is set in the Belt speed section of Measurement configuration then belt speed will be forced to zero when this signal is not set. This is intended for use with a fixed speed setting but will work for any speed source.
Reset totals: a rising edge or 0 > 1 transition on this signal will reset cumulative volume/mass totals to zero. For idle state measurement this has the same effect as pushing the Reset button on the Dashboard. If a job is running this is the same as resetting the active job on the Active job page.
To assign a control signal to an input channel, click on the Add button in the Control signal inputs section of Inputs/Outputs and select the required control signal. This creates a new row for the selected signal. Click in the mapping area of this row to select an available input channel. A control signal can only be mapped to one input channel.
Modbus coils: coils must be defined before they can be selected as an input channel (see 2.5 Modbus TCP Server Configuration).
Digital switching inputs: If the control signal is not a pulse type input the Active high checkbox can be un-checked when adding the channel to invert the digital input logic. This setting can be edited at any time by clicking on the settings icon () on the assigned channel. See LoadScan CVS-I/O Installation Guide document for signal requirements and wiring.
2.4.2 Status signal outputs
The following status signals can be sent to external monitoring and control systems or directly control belt start/stop, activate status indicator lights and so on. These can be written to Modbus discrete inputs or drive digital switching outputs:
- Idle: measurement mode is operational, but no job is active (unassigned measurement only).
- Job active: a job is running. This signal can be used, for example, to start the belt automatically when a job is started and stop the belt when the job is stopped.
- Job target reached: target volume/weight for the active job has been reached and the job is still running. This signal can be used, for example, to control a visual indicator to advise the operator that the job is ready to be manually stopped.
- Black belt: belt is running (belt speed greater than zero) but there is no material on the belt.
- Belt stopped: belt speed is zero.
- Warning: non-fatal error condition requiring operator intervention is active.
- Error: a fatal error condition requiring operator intervention is active (measurement stopped).
To assign a status signal to an output channel, click on the Add button in the State outputs section of Inputs/Outputs and select the required status signal. This creates a new row for the selected signal. Click in the mapping area of this row to select an available output channel. One status signal can be assigned to multiple output channels. Multiple status signals can also be assigned to one output channel. In this case an output will be active when any of the assigned status signals are set.
Modbus discrete inputs: discrete inputs must be created before they can be selected as an output channel (see 2.5 Modbus TCP Server Configuration).
Digital switching outputs: The Active high checkbox can be un-checked when adding the channel to invert the digital output logic. This setting can be edited at any time by clicking on the settings icon () on the assigned channel. See LoadScan CVS-I/O Installation Guide document for signal requirements and wiring.
2.4.3 Control value inputs
The following control values can be supplied by external control systems. They can be read from Modbus holding registers or 4-20 mA current loop analogue inputs:
- Belt speed: If speed source is set to Belt speed input in the Belt speed section of Measurement configuration then this value sets the belt speed.
To assign a control value to an input channel, click on the Add button in the Control value inputs section of Inputs/Outputs and select the required control value. This creates a new row for the selected value. Click in the mapping area of this row to select an available input channel. A control value can only be assigned to one output.
Modbus holding registers: holding registers must be created before they can be selected as an input channel (see 2.5 Modbus TCP Server Configuration).
Analogue inputs: the control values corresponding to the 4 mA and 20 mA end-points must be specified at the time of adding the channel and can be edited at any time by clicking on the settings icon () on the assigned channel. See LoadScan CVS-I/O Installation Guide document for analogue input signal requirements and wiring.
2.4.4 Measurement value outputs
The following measurement values can be sent to external monitoring and control systems. They can be written to Modbus input registers or 4-20 mA current loop analogue outputs:
- Cumulative volume: the current total volume
- Cumulative mass: the current total weight
- Volume flow rate: the current volume flow rate
- Mass flow rate: the current mass flow rate
- Belt speed: the current belt speed
- Load height: the current load height
- Load position: the current load position
To assign a measurement value to an output channel, click on the Add button in the measurement outputs section of Inputs/Outputs and select the required measurement. This creates a new row for the selected measurement. Click in the mapping area of this row to select an available output channel. One measurement value can be output to multiple output channels, but a single output channel can only be assigned to one measurement.
Modbus input registers: input registers must be created before they can be selected as an output channel (see 2.5 Modbus TCP Server Configuration).
Analogue outputs: the control values corresponding to the 4 mA and 20 mA end-points must be specified at the time of adding the channel and can be edited at any time by clicking on the settings icon () on the assigned channel. See LoadScan CVS-I/O Installation Guide document for analogue input signal requirements and wiring.
2.5 Modbus TCP Server Configuration
Live measurement values, status signals, control values and control signals can be mapped to Modbus registers. Modbus TCP Server settings are available in the Modbus TCP Server section of System Configuration. This document assumes the reader is familiar with Modbus TCP. The image below shows an example configuration only.
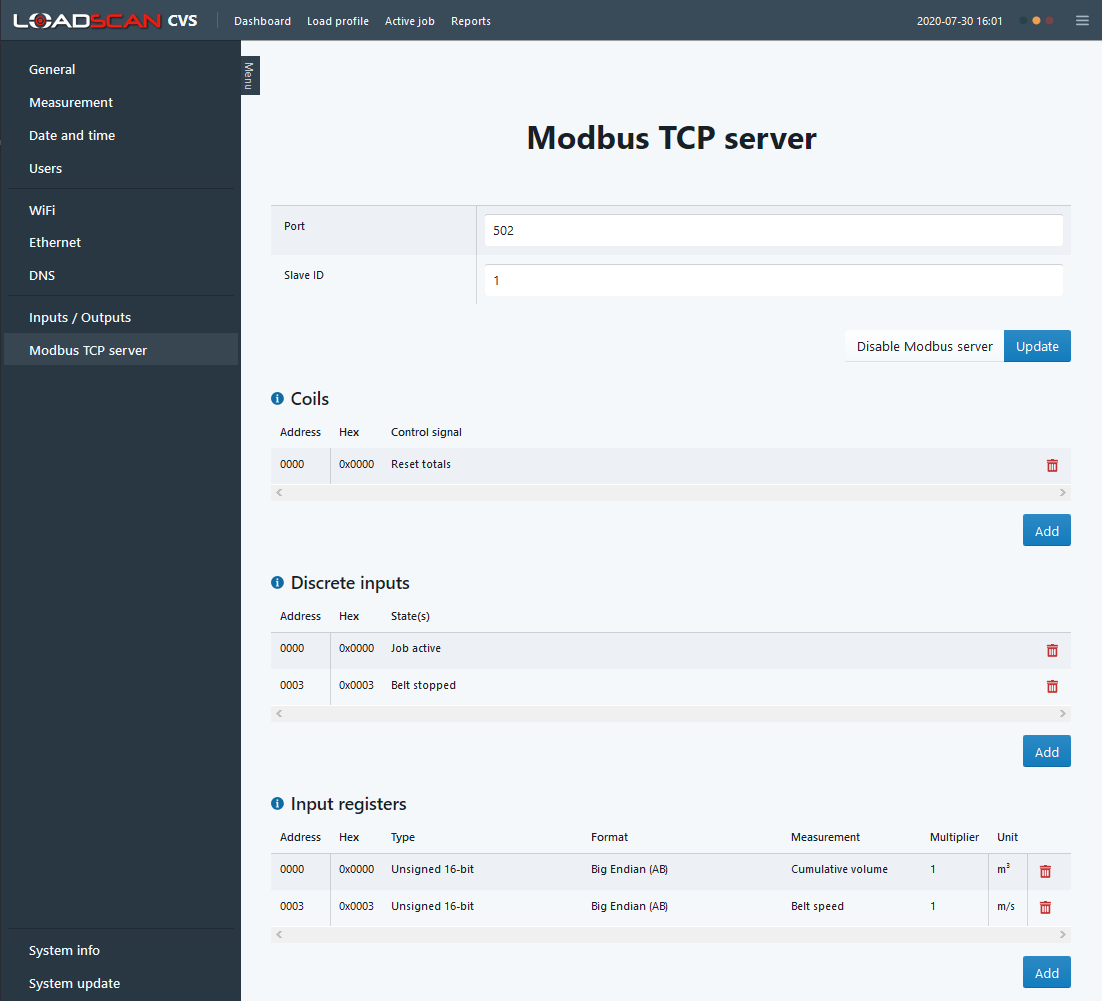
Modbus configuration is very flexible. The CVS does not have a fixed register table. Modbus registers can be added and removed as required. Register addresses can also be set as desired and multiple data formats are available.
The Modbus TCP server must be enabled with the Enable Modbus server button and can be disabled at any time without losing existing configuration.
Once Modbus registers have been defined, they can be used as input or output channels and assigned to different measurement or control values or signals (see 2.4 Input/Output Configuration).
The following Modbus register types can be added:
- Coils: these are discrete CVS inputs (outputs from remote Modbus TCP client) and can be assigned to control signal inputs.
- Discrete inputs: these are discrete CVS outputs (inputs to remote Modbus TCP client) and can be assigned to status signals.
- Holding registers: these are value inputs to the CVS (outputs from remote Modbus TCP client) and can be assigned to control values. Multiple data formats are available, and a divider can optionally be applied to the value read from a holding register.
- Input registers: these are CVS outputs (inputs to remote Modbus TCP client) and can be assigned to measurement values. Multiple data formats are available, and a multiplier can optionally be applied to the value before writing to an input register.
To add a Modbus register, click the Add button for the required type and enter the requested details in the pop-up dialog. After Modbus objects have been created, they automatically appear in the Input/Output section of System Configuration, with the selected signal or value assignment. A Modbus register can be re-assigned to a different signal or value or the assignment removed. Removing the assignment in Input/Output configuration clears the assignment but does not remove the Modbus register from Modbus TCP Server configuration. It can be removed from Modbus TCP Server configuration or re-assigned in Input/Output configuration.